摩擦材料用铁粉【返回上级】
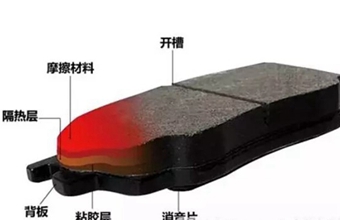
铁粉在摩擦产品中的核心作用
◆ 摩擦性能调节
摩擦系数稳定性:铁粉具有较高的硬度和耐高温性,能够在刹车过程中提供稳定的摩擦系数,减少“热衰退”现象(高温下摩擦性能下降)。
磨损控制:铁粉通过与其他材料(如石墨、铜粉)的协同作用,平衡摩擦材料的磨损率,延长使用寿命。
◆ 热管理
导热性:铁粉的高导热性有助于快速将摩擦产生的热量从接触面导出,避免局部过热导致刹车失效。
耐高温性:铁基材料在高温下仍能保持结构稳定性,减少材料因热膨胀或氧化导致的性能劣化。
刹车片材料配方中的铁粉应用
◆ 成分比例
铁粉在摩擦材料中的占比通常为 30%-70%,具体取决于刹车片类型(如低金属配方、半金属配方)。
低金属配方:铁粉+少量铜粉+石墨+陶瓷纤维,用于普通乘用车,噪音较低。
半金属配方:铁粉为主(50%以上)+钢纤维+石墨,适用于重载车辆,耐高温性更强。
◆ 与其他材料的协同
石墨/二硫化钼:作为润滑剂,减少刹车噪音和磨损。
陶瓷纤维/芳纶纤维:增强材料韧性,防止开裂。
铜粉(逐步被替代):传统配方中用于提升导热性,但因环保法规(如欧盟REACH)逐渐被铁基材料替代。
粉末冶金工艺的关键步骤
◆ 原料混合
铁粉与其他成分(粘结剂、润滑剂、增强纤维)均匀混合,确保摩擦性能的一致性。
◆ 预压成型
混合粉末通过模具压制成型,形成刹车片毛坯,密度控制在 5.5-6.5 g/cm³。
◆ 高温烧结
铁粉刹车片的性能优势
◆ 高性价比
铁粉成本显著低于铜粉,且来源广泛,适合大规模生产。
◆ 环保合规性
符合无铜化趋势(如欧盟要求刹车片铜含量<5%),铁基材料成为主要替代方案。
◆ 综合性能平衡
耐磨性:铁粉硬度高,减少磨损。
抗热衰退:在连续刹车工况下仍能保持性能稳定。
噪音控制:通过添加石墨等材料抑制振动噪音。
◆ 摩擦性能调节
摩擦系数稳定性:铁粉具有较高的硬度和耐高温性,能够在刹车过程中提供稳定的摩擦系数,减少“热衰退”现象(高温下摩擦性能下降)。
磨损控制:铁粉通过与其他材料(如石墨、铜粉)的协同作用,平衡摩擦材料的磨损率,延长使用寿命。
◆ 热管理
导热性:铁粉的高导热性有助于快速将摩擦产生的热量从接触面导出,避免局部过热导致刹车失效。
耐高温性:铁基材料在高温下仍能保持结构稳定性,减少材料因热膨胀或氧化导致的性能劣化。
刹车片材料配方中的铁粉应用
◆ 成分比例
铁粉在摩擦材料中的占比通常为 30%-70%,具体取决于刹车片类型(如低金属配方、半金属配方)。
低金属配方:铁粉+少量铜粉+石墨+陶瓷纤维,用于普通乘用车,噪音较低。
半金属配方:铁粉为主(50%以上)+钢纤维+石墨,适用于重载车辆,耐高温性更强。
◆ 与其他材料的协同
石墨/二硫化钼:作为润滑剂,减少刹车噪音和磨损。
陶瓷纤维/芳纶纤维:增强材料韧性,防止开裂。
铜粉(逐步被替代):传统配方中用于提升导热性,但因环保法规(如欧盟REACH)逐渐被铁基材料替代。
粉末冶金工艺的关键步骤
◆ 原料混合
铁粉与其他成分(粘结剂、润滑剂、增强纤维)均匀混合,确保摩擦性能的一致性。
◆ 预压成型
混合粉末通过模具压制成型,形成刹车片毛坯,密度控制在 5.5-6.5 g/cm³。
◆ 高温烧结
在 900-1100°C 的惰性气氛中烧结,使铁粉颗粒间形成冶金结合,提升强度。
◆ 后处理
表面开槽或倒角,优化摩擦接触面;部分刹车片需喷涂消音涂层。铁粉刹车片的性能优势
◆ 高性价比
铁粉成本显著低于铜粉,且来源广泛,适合大规模生产。
◆ 环保合规性
符合无铜化趋势(如欧盟要求刹车片铜含量<5%),铁基材料成为主要替代方案。
◆ 综合性能平衡
耐磨性:铁粉硬度高,减少磨损。
抗热衰退:在连续刹车工况下仍能保持性能稳定。
噪音控制:通过添加石墨等材料抑制振动噪音。